What is Metal Manufacturing: From Raw Materials to Finished Products
- Metal Stamping |
- Jun 5, 2025
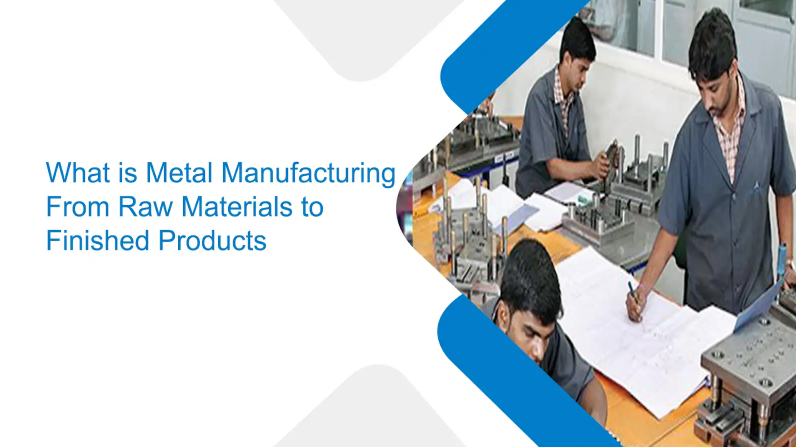
Metal manufacturing is one of those foundational industries we rarely think about, yet it’s all around us. From the bridges we drive on to the phones in our hands, metals are everywhere, shaped, cut, moulded, and engineered into structures and products we rely on every day. But what does the journey from raw ore to a finished metal product look like?
In this blog, we’ll take a closer look at what metal manufacturing involves, how raw materials are transformed into usable components, and the role sheet metal fabrication companies and advanced fabrication methods play in shaping today’s metal manufacturing landscape.
Understanding Metal Manufacturing
At its core, metal manufacturing refers to the process of converting raw metal materials, like iron, aluminium, copper, and steel, into finished goods. These can range from small precision parts to large structural frameworks. The process is intricate, multi-staged, and often highly customised depending on the end use of the product.
Whether it’s automotive components, aerospace parts, medical devices, or industrial machinery, the principles of metal manufacturing remain largely the same: extract, process, fabricate, assemble, and finish.
The Journey Begins: Raw Materials
Every metal product starts with raw materials. These are either mined directly from the earth in the form of metal ores or recycled from previously used metals.
- Iron ore is the primary source of steel.
- Bauxite is refined into aluminium.
- Copper is mined and refined for its excellent electrical conductivity.
After extraction, these raw materials undergo multiple purification and processing phases to transform into usable metals. The refinement process depends on the type of metal, but it generally involves smelting, casting, or electrolytic extraction.
Primary Metal Processing
After extraction, the raw metal is refined into ingots, slabs, or coils. This is the stage at which the metal becomes workable. At this point, manufacturers decide on the form factor, such as sheets, bars, rods, or wires, based on the product requirements.
Techniques used here include:
- Casting – Pouring molten metal into moulds.
- Rolling – Reducing thickness or forming shapes using rollers.
- Extrusion – Forcing metal through a die to create specific profiles.
These semi-finished products are now ready for fabrication and detailed shaping.
Shaping the Product: Metal Fabrication
This is where things start getting specific. Metal fabrication involves transforming basic metal forms into detailed parts, assemblies, or finished products. It’s also the stage where sheet metal fabrication companies play a huge role.
Some standard fabrication techniques include:
- Cutting – Using laser, plasma, waterjet, or mechanical methods.
- Bending – Forming metal sheets or bars into desired angles using press brakes or rollers.
- Welding – The process of joining two or more pieces of metal together.
- Punching and stamping – Creating holes, indentations, or custom patterns.
The level of precision in fabrication has dramatically improved with the rise of CNC (Computer Numerical Control) machining, enabling manufacturers to create complex designs with minimal human error.
Assembly and Joining
Once individual parts are fabricated, they need to be joined into functional units. This step may involve:
- Mechanical fastening (screws, bolts, rivets)
- Welding or brazing (for permanent joints)
- Adhesive bonding (for lighter materials or mixed-material components)
The assembly phase ensures the product works as intended, especially in sectors where tolerances are tight and performance is non-negotiable, such as aerospace, defence, and medical equipment.
Surface Finishing and Quality Control
Before any metal product leaves the manufacturing floor, it undergoes surface treatments and quality checks. This final touch is more important than it might seem. A good surface finish not only improves appearance but also adds durability, corrosion resistance, and in some cases, enhanced performance.
Common surface finishing processes include:
- Powder coating
- Anodising
- Electroplating
- Polishing and brushing
Quality control teams then step in to ensure every product meets the required standards. Using tools such as coordinate measuring machines (CMMs), ultrasonic testing, and visual inspections, manufacturers verify everything from dimensional accuracy to structural integrity.
Types of Metal Products Made
With a wide range of processes and tools, metal products manufacturing serves numerous industries. Some standard products include:
- Structural components – Beams, columns, support frames
- Automotive parts – Chassis, panels, gears
- Consumer goods – Kitchen appliances, tools, electronics casings
- Medical instruments – Surgical tools, imaging equipment frames
- Aerospace parts – Aircraft panels, brackets, turbine components
Role of Sheet Metal Fabrication Companies
Sheet metal is a preferred material across industries because it’s lightweight, strong, and easy to shape. Sheet metal fabrication companies specialise in working with thin, flat metal sheets to produce a wide range of products, including enclosures, cabinets, panels, and ducts.
These companies bring a unique set of skills and equipment to the table, including:
- Laser cutting machines
- Precision press brakes
- High-speed CNC punch presses
- Finishing and assembly capabilities
Due to their specialisation, they’re often able to produce complex, customised components faster and more cost-effectively than general manufacturers.
Evolving with Technology
The world of metal manufacturing is constantly evolving. Today’s leading metal manufacturing companies are embracing Industry 4.0, a combination of automation, data analytics, and digital connectivity that improves efficiency and reduces waste. Robotics, AI-powered quality checks, and predictive maintenance are no longer futuristic concepts; they’re being implemented right now.
This not only ensures better outcomes but also opens the door to innovation in product design and manufacturing methods.
Final Thoughts
Metal manufacturing is far more than just bending steel or cutting sheets. It’s a deeply technical, creative, and essential industry that continues to shape our modern world. From raw ores extracted from the ground to finely finished parts in aerospace engines or medical devices, each step in the metal manufacturing process is driven by expertise, precision, and innovation.
Whether you’re looking to understand the process or work with a reliable metal manufacturing company, knowing the stages from material selection to final inspection can give you a clearer picture of how metals fuel the infrastructure, machines, and technology around us.
FAQs
Q1. What is metal manufacturing?
Metal manufacturing is the process of converting raw metals, such as iron, aluminium, and copper, into finished products through stages including processing, fabrication, and finishing.
Q2. What are the key steps in metal manufacturing?
The main steps include raw material extraction, primary processing (casting, rolling, extrusion), fabrication (cutting, bending, welding), assembly, and surface finishing.
Q3. Why are sheet metal fabrication companies important?
They specialise in shaping thin metal sheets into precise, custom parts using advanced equipment, such as laser cutters and CNC machines, often improving speed and cost efficiency.
Q4. What industries rely on metal manufacturing?
Industries such as automotive, aerospace, medical devices, construction, and consumer goods all depend heavily on metal manufacturing for components and structures.
Q5. How is technology changing metal manufacturing?
Modern advancements, such as Industry 4.0 automation, AI-powered quality control, robotics, and predictive maintenance, make metal manufacturing more efficient, precise, and innovative.