Cost-Saving Strategies in Metal Stamping Tool and Die Manufacturing
- Metal Stamping |
- Apr 11, 2025
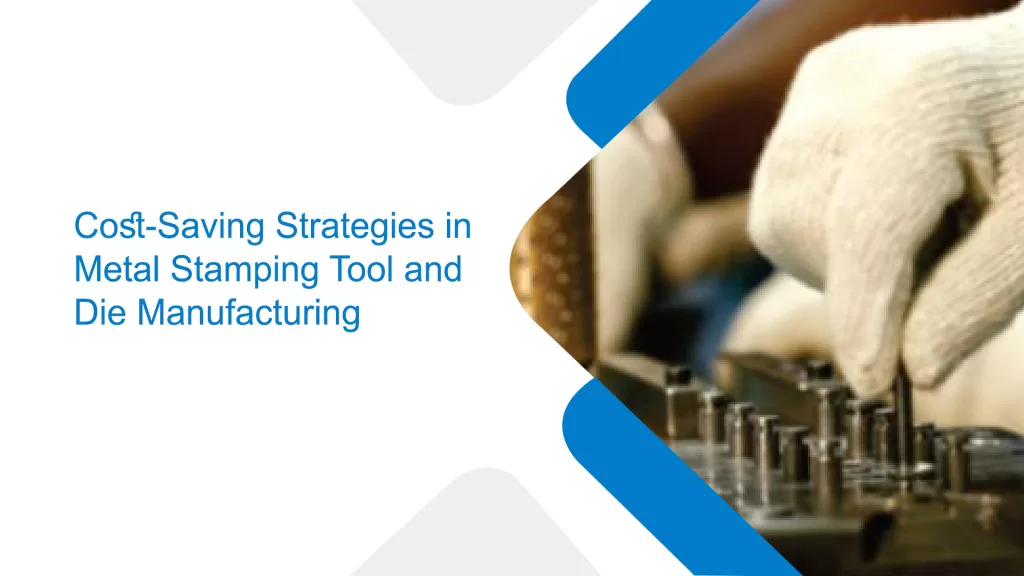
A wide range of elements can influence the total cost of precision-stamped metal parts. The cost of materials and die equipment is a significant contributor. In industries with narrow margins and severe competition, cost-cutting methods are beneficial and required for long-term success.
The businesses must have access to quality metal stampings at affordable prices. Tool and die savings require selecting a manufacturing partner who balances value and affordability. But how do manufacturers help you save money on metal components? Let us find out the points mentioned below.
Design Optimization
The design of the parts is one of the most significant elements to consider when considering cost reductions on die stamping. The experience of the manufacturer is essential in this process. The most efficient cost-cutting strategy is to prioritise designs that cost less. Symmetrical designs are frequently less expensive, and removing extraneous shapes and features can help save production time and tooling costs.
Sometimes, manufacturing partners can go one step further by standardising parts used in various assemblies and productions. This can lessen the production cost. Prototyping and testing are other areas of attention for many manufacturers. Funding early prototypes during the design stage allows possible problems to be found before production. This helps manufacturers to prevent subsequent expensive tooling changes and redesigns.
Material Efficiency
To keep costs under control, the right manufacturing partner can assist in improving material efficiency. This starts with material selection. Choosing a material that fits the performance criteria is crucial. It should also go well within your budget. The best quality material can reduce maintenance and last longer.
There are several options for manufacturers to cut costs during manufacturing. Experienced manufacturers can strategically design equipment to reduce scrap and optimise the cutting and forming operations. Reducing the thickness of the material or selecting a thinner gauge are also effective ways to cut costs without compromising quality. You can make better choices with the help of manufacturers.
Advanced Manufacturing Technologies
Significant cost savings can be achieved using modern technologies for sustainable die manufacturing. It includes wire EDM and CNC machining. Fewer defective dies are produced, and rework expenses are decreased because CNC machining guarantees accuracy and consistency. Wire EDM reduces material stress and waste while enabling the complex cutting of hard metals. It is especially helpful for producing intricate shapes that conventional machining methods would not be able to make or would be prohibitively expensive.
The manufacturing has considerable promise for producing intricate inserts and progressive tool sheet metal more quickly and affordably than conventional techniques. More effective equipment may involve an initial outlay of funds, but it can significantly lower expenses and usage over time.
Tooling and Die Efficiency
Investing in high-quality metal stamping tool and die design may minimise errors and the need for rework while ensuring accurate and consistent production. Tool and die savings can result from carefully making the die process. Additionally, more robust instruments need less upkeep and might lower replacement expenses.
In light of this, routine maintenance can assist in decreasing downtime, prolonging the life of dies and tools, and preventing unplanned malfunctions. Manufacturers can also use data and technology to optimise the die. CAD, sensor technologies, and monitoring systems can trade operations, enhance precision, minimise errors, and help providers make more informed decisions.
Workforce Training and Skill Development
A trained workforce can greatly impact cost-effectiveness. By ensuring that machinists and maintenance personnel are knowledgeable about the newest methods and technology, proper training helps to reduce mistakes and inefficiencies. The workforce is kept current by promoting lifelong learning and making certifications.
Investing in apprenticeships also guarantees a consistent flow of skilled workers who can uphold high standards without incurring the exorbitant fees frequently connected with recruiting outside experts. An informed workforce is better equipped to spot possible savings opportunities, enhance workflows, and develop creative solutions that could otherwise go unnoticed.
Better Outsourcing Strategy
It is not necessary to manufacture every die or tool in-house. Outsourcing can result in substantial cost reductions with careful planning. Because of economies of scale, it is frequently possible to outsource low-complexity components to specialist companies that can create them more cheaply.
Quality shouldn’t be sacrificed for outsourcing to guarantee that outsourced parts are seamlessly integrated into the manufacturing process. Better communication, more collaborative innovation, and preferred pricing might result from establishing long-term relationships with reliable suppliers.
Summing It Up
To buy the best quality metal stamping tool and die, you can rely on Eigen Engineering. We offer the best quality die designs at an affordable price. We supply raw materials for various industries. We serve a wide range of global sectors and take care to be early adopters of emerging technologies. Our track record of reliability and innovation guarantees that they will play a significant part in determining the direction of engineering in various fields. Contact us today to get the best quality metal stamping tools.