Metal Electroplating: An Expert Guide to the Process
- Plating |
- May 24, 2022
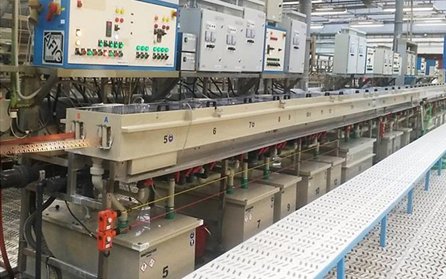
Electroplating is a widely utilized metal finishing and improvement technique used in metal stamping manufacturing industry to make the metal parts visually appealing and improve their efficiency.
Despite its prevalence, relatively few people outside the industry are acquainted with electroplating, what it is, and how it works. If you’re contemplating electroplating for your next manufacturing process, it’s critical to understand how the process works and the material and process alternatives accessible to you.
What is Electroplating?
Electroplating includes depositing material with the aid of an electric current. This method deposits a thin coating of metal onto the surface of a workpiece referred to as the substrate. Electroplating is often used to change the physical properties of an item. This procedure may enhance the wear resistance, corrosion resistance, aesthetic appeal of things, and thickness.
Electroplating was adopted and developed across Europe due to Brugnatelli’s studies. While electroplating may seem to be cutting-edge technology, the technique dates back to the Middle Ages. Electroplating was originally tested in the early 18th century, and Brugnatelli standardized the method in the first half of the nineteenth century. Over the following two centuries, as industrial processes progressed due to the Industrial Revolution and two world wars, the electroplating process changed to meet demand, culminating in the technology used by Sharretts Plating Company today.EXPLORE OUR ELECTROPLATING SERVICES
Electroplating Process
During the electroplating process, a metal dissolves in an electrolytic solution and deposits on a metal surface in the presence of an electric current.
- The metal that gets deposited on the other metal is chosen as an anode. For example, in the electroplating nickel process, nickel will serve as the anode or the positively charged component.
- The metal that requires coating is connected as a cathode in the circuit. The ions pass through the electrolytic solution from the anode and deposit on the cathode.
- Both metals are immersed in an electrolytic solution that promotes the passage of electricity, the solution includes one or more metal salts, most often copper sulphate.
- The process starts when power is connected to the circuit and it starts generating electric current.
Also Read- A Step By Step Guide For Copper Electroplating Solution
The electric current oxidizes the metal, enabling metal atoms to dissolve as positive ions in the electrolyte solution. The current causes the metal ions to migrate to the negatively charged substrate and deposit a thin metal coating onto the item.
Consider the plating services of gold onto metal jewellery as an example. The gold-plated metal serves as the anode in the circuit, while the metal jewellery serves as the cathode. Both are dissolved in solution, and DC electricity is applied to the gold to cause it to dissolve. Gold atoms that have been dissolved attach to the surface of the base metal jewellery, forming a gold coating.
While this procedure is continuous, three variables may affect the plating’s quality:
- Bath conditions like Bath temperature and chemical composition
- Distance between both electrodes
- Time and voltage of electric current
Benefits Of Electroplating
Electroplating has several advantages for components. Among the many advantages of electroplating are the following:
- Protective barrier: Electroplating provides a barrier between the substrate and the environment. This barrier may, in certain situations, protect against corrosion induced by the environment. These distinct advantages because they endure longer in harsher environments and require less frequent replacement.
- Improved appearance: Exterior components are often coated with small layers of precious metals to increase their lustre and aesthetic appeal without high additional expenditures. It also protects silverware against tarnishing, increasing its lifespan and aesthetic look over time.
- Electrical conductivity: Silver and copper plating improve electrical conductivity in parts, providing a cost-effective and efficient method of conducting electricity in electronics and electrical components.
- Resilience to high temperatures: Several metals, notably gold and zinc-nickel, are resistant to high temperatures, enhancing the substrate’s resistance to heat damage. It, in turn, may extend the life of plated components.
- Increased hardness: Electroplating enhances the strength and durability of substrate materials. The coating makes them more resistant to damage caused by stress or harsh handling and assists in extending the life of the plated component.
Some advantages are metal-specific. Nickel plating, for example, is beneficial for minimizing friction, which helps to reduce wear and tear and extends the life of parts.
Determining the most efficient production method is critical to manufacturing efficiency. Electroplating is a cost-effective and beneficial solution for many applications, but you must work with the proper plating business to get the full advantages.
Eigen’s electroplating nickel services ensure the metal parts incur all the benefits and remain lustrous for a long time. Our expert team picks up the appropriate services to suit the metal part application.
Ujjwal handles crucial roles like AGM Marketing, researcher, and is an author for KDDL – Eigen. He currently works with Eigen for implementing proven techniques and strategies for marketing plans on online and offline platforms. An expert in efficiently executing SEO, SEM, email marketing, social media marketing, PR marketing, Print campaigns, etc. Ujjwal has coordinated an efficient marketing team on various creative campaigns and programmatic buying to support various digital cross-promotion efforts. Implement efficient search optimization strategies with the help of collateral material and metrics.
In his former years, Ujjwal has years of experience in a managerial role for several reputed companies. His years of experience combined with the flair of writing help him come up with result oriented strategies for Eigen.