Metal Plating Exploring Various Types And Techniques
- Plating |
- Apr 23, 2024
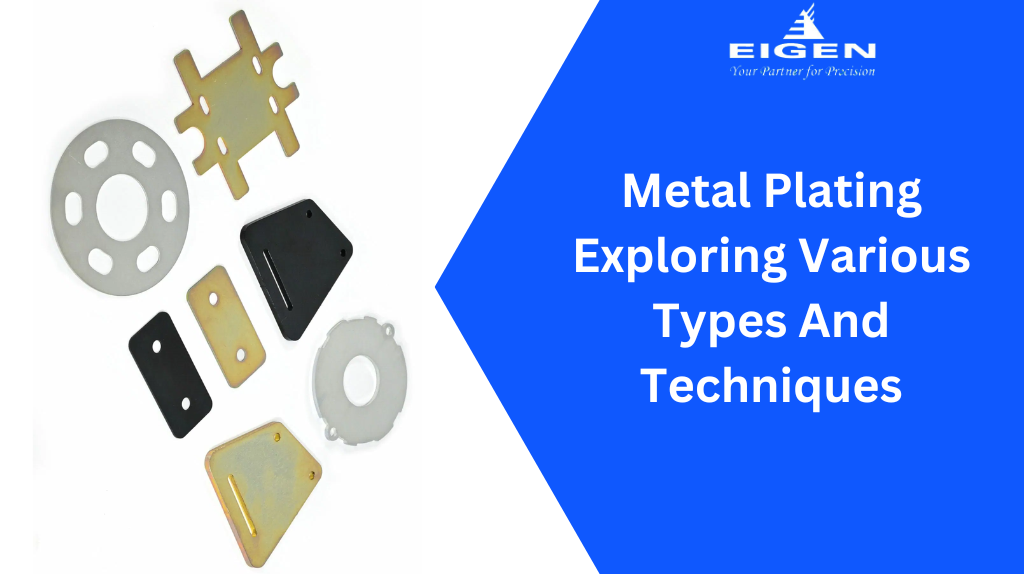
Customized parts manufacturers utilize various metal plating treatments to meet various industrial needs today. Most of these metal plating surface treatments provide parts with a cleaner appearance and also increase functionality.
Metal plating is a great option for many applications since it is a significant component of contemporary technology and a viable alternative for post-production finishing. This article examines the fundamentals of metal plating services and outlines the methods, so read below to know more.
Different Types of Metal Plating
There are several common industrial metal plating finishes for metals to choose from; these are the types:
Zinc Plating: When it comes to producing galvanized metal on metal substrates, zinc is one of the most affordable materials. You have more control over thickness and uniformity when using the zinc plating technique since it creates a very ductile layer on plated metal.
Chrome Plating: An overlay is applied to the metal components using chrome plating. The main goal of chrome plating is to improve the material’s appearance. The chrome-plating process is also similar to the nickel-plating process and is used for the same purposes at times. Tolerances on worn-out parts can be restored with chrome plating.
Nickel Plating: Nickel plating contributes to the protective coating, cosmetic enhancement, and wear resistance of household items, including shower fixtures, cutlery, and doorknobs. Copper and aluminum can both be plated using the nickel plating technique. On other metals, though, it functions admirably, providing chromium with a basic coating.
Copper Plating: Copper plating is a plating that offers high conductivity at a comparatively lower cost. Copper plating is the standard for electronic equipment like circuit boards. Copper plating uses the same technique as electroless nickel plating, as both are done without external current.
Cadmium Plating: On several base metals, including iron, steel, copper, and aluminum, cadmium plating is applied as a thin, metallic coating. Its chemical resistance, ease of solderability, corrosion resistance, and malleability are all rather excellent.
Silver Plating: If electrical conductivity is an important consideration, silver plating is a great metal finish option. Silver metal plating services for plating copper-based products are an affordable option.
Gold Plating: Applications that require good oxidation resistance and strong electrical conductivity use the gold plating method. It has a wide range of uses, including improving electrical connector conductivity and other electronic components.
Tin Plating: A solderable tin layer coating is applied to a material’s surface using electrical current to do this industrial finish. Tin is much more affordable to electroplate than other metals like gold, palladium, or platinum and is, therefore, a more cost-effective method.
Rhodium Plating: Another common metal plating technique is rhodium plating, which applies a thin layer of rhodium to the surface of jewelry. The rhodium flashing or dipping technique is the same as this one. It aids in enhancing a piece of jewelry’s shine, robustness, and light reflection.
Metal Plating Techniques
Diverse industries employ different methods of metal plating techniques; these are those techniques:
Electroplating: A metal or metal alloy is deposited on a workpiece’s surface using the metal plating method known as electroplating. The physical, mechanical, and chemical qualities of a workpiece are improved by electroplating. One electroplating type that gives the plated metal a uniform, fast-drying coating is the gold plating method. On the metallic workpiece, this thin coating creates an attractive and protective surface.
Electroless Plating: The best substitute for electroplating is the electroless plating method, which is also significantly more affordable and straightforward. Electroless plating uses a reducing chemical solution to deposit metals on the surface of various materials, including copper, gold, nickel, and silver. The electroless nickel plating method is used in the production of components by the electrical & automotive industries. The electroless plating method is also used to make precision metal stampings, which are a useful component in electronics.
Immersion Plating: To perform immersion metal plating, a metal is submerged in a chemical solution containing noble metal ions. Furthermore, only noble metals like platinum, silver, and gold are appropriate for it.
Carburizing: The metal plating technique called carburizing hardens a metal’s surface while leaving the metal underneath malleable. As a result, on the surface case, a solid, thinner layer of metal is formed. Product designers can effectively prevent corrosion in metal-using industries by using carburizing as a metal plating process.
Physical Vapor Deposition: To create a thin layer for this metal plating technique, atoms from a material source are first vaporized and then deposited onto a substrate surface using low-pressure gas or plasma.
The fundamental techniques in physical vapor deposition are arc plasma plating, vacuum evaporation, ion plating, and sputtering deposition. PVD coating offers great diffraction, high adhesion, quick deposition, and a wide range of applications.
Plasma Spray Coating: Heat-softened melted components are sprayed on a material’s surface to produce the desired coating in this metal plating process. Applications for plasma spray include protecting jet engines, refurbishing worn parts, and other things. Excellent resistance to heat, oxidation, wear, abrasion, and electricity is provided by the plasma spraying technique.
Read More: How Metal Plating Enhances Precision Stamped Parts?
Final Thoughts
Hopefully, you have now gained an idea about the metal plating processes. If you want to find a reliable company for your industrial needs, search metal stamping company near me online.
Ujjwal handles crucial roles like AGM Marketing, researcher, and is an author for KDDL – Eigen. He currently works with Eigen for implementing proven techniques and strategies for marketing plans on online and offline platforms. An expert in efficiently executing SEO, SEM, email marketing, social media marketing, PR marketing, Print campaigns, etc. Ujjwal has coordinated an efficient marketing team on various creative campaigns and programmatic buying to support various digital cross-promotion efforts. Implement efficient search optimization strategies with the help of collateral material and metrics.
In his former years, Ujjwal has years of experience in a managerial role for several reputed companies. His years of experience combined with the flair of writing help him come up with result oriented strategies for Eigen.