Proper Planning in Metal Stamping can Save Time and Cost
- Precision Metal Stamping |
- Oct 31, 2017
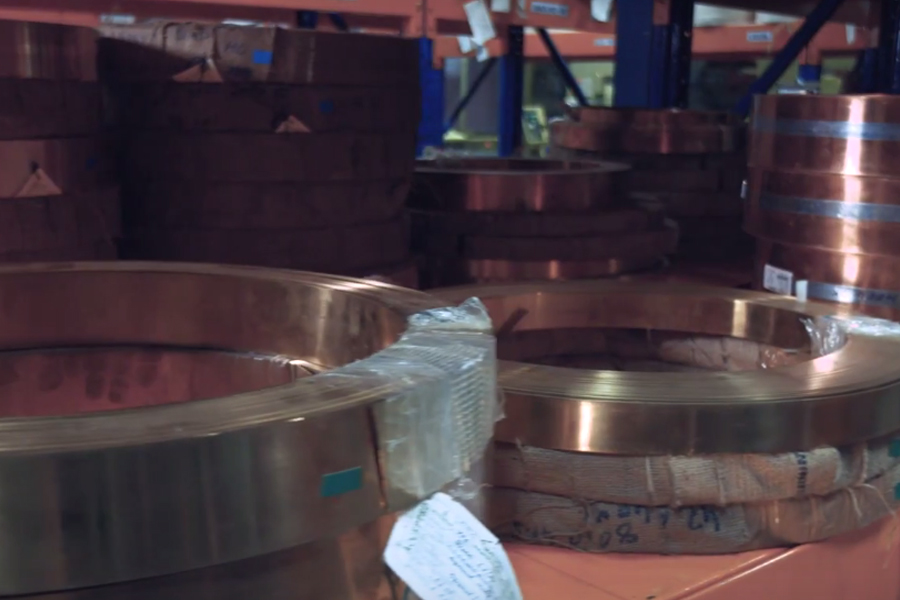
Precision metal stamping is complex, and different processes are needed to bring out the best results. Careful planning by the metal stamping company along with an efficient team of engineers is what will help ensure cost-effective results. The stamping supplier needs to put forth every effort to make sure that the new stamping is designed efficiently when it comes to material usage and the final assembly process. It is crucial to have a proper estimation of the fluctuation in demand for the product, and then allow time for secondary operations. The below mentioned points are highly beneficial in this regard.
- Contents hide
Consider the final assembly dimensions
It is important to assess the dimensions for the final assembly. These dimensions are critical if there is another part that needs to snap into place with the metal stamping. The critical dimensions need to be assigned accurate measurements and should be meticulously highlighted on the drawing. The metal stamping company follows all the set processes and design in-die assemblies to complete the production on time and with efficient results. A reliable and experienced company designs the metal stamping dies in order to eliminate unnecessary steps in assembly, and save time and labor cost. The orientation of stamped part, the packaging, and other such custom options can be planned for the final assembly so that the end result is efficient and benefits the customers.
Importance of accurate production volumes
It is a good practice for precision metal stamping companies to set realistic annual production volumes well before time. If there are variations expected throughout the year, then the metal stamping team needs to have a flexible schedule. In order to meet the forecast demand, the stamping companies will also need to have a proper inventory of parts. The anticipated production volumes, along with specific client requirements will help the metal stamping company to decide whether to go for manual assembly or automated assembly to handle multiple components. For example, if there is a new product launch where demand can increase quickly, it may be a cost-effective solution to start with automation.
On the other hand, if the demand is going to increase above the production capabilities, the company can then prepare to implement other strategies to use their machineries efficiently or design a die for great results.
Selecting the best material
The experienced engineers in a precision stamping company can recommend the best material for long term functions. Based on their expertise in this field and the experience of working with different materials, the engineers can assist in choosing materials such as noble metals, and pre-plated alloys to beryllium copper depending upon the application. In order to validate the performance, various metals can be tested during the prototyping and simulation. The standard lead times for different materials may vary depending on the supply and demand, and according to the availability of the metals in the market. One the best material is selected for a project, the metal stamping company can implement the right strategies to make efficient use of the same.
Different materials used in metal stamping
Ferrous metals
- High-tensile steel
- Stainless steel
- Hot-rolled and cold-rolled steel
- Low, medium, and high carbon steel
- Coated steel
- Spring steels
Non ferrous metals
- Brass
- Aluminum alloys
- Copper
- Aluminum
- Aluminum-clad copper
- Phosphor bronze
- High nickel alloys
- Beryllium copper
Noble metals
- Gold
- Titanium
- Niobium
- Iridium
- MP35N
- Platinum
Depending upon the project, the metals need to be procured much in advance. Some of the metals are easily available on the market, but there are some that need time and special orders need to be placed. So, the company should plan well in advance and procure the material according to the demand.
Planning for secondary operation
After the stamping is complete, there are also secondary operations that the supplier needs to consider. In order to speed up the cycle time, these operations need to be scheduled well in advance so that these can be handled as soon as possible. The planning will not just include areas such as plating or assembly and shipping, but proper quality control as well. The quality control implemented in different processes will ensure that the final product is of great quality.
Eigen is way ahead in Planning
Proper planning is important to get the right results in every project, and also to cut down on the unnecessary processes. At Eigen, we realize that a proper plan should also be flexible, depending upon the market condition. We are open to make changes depending upon where we are in the project, what are certain problems we face and also, and if changes are made to the plan we instantly communicate it with the entire team. For example, there might be increased demand for a particular component, and so we need to make the relevant changes in the schedule so that the other operations are not affected. The proper planning at Eigen, not only helps to save on cost, but this also helps us derive efficient results. We always strive to give our clients the best possible services, and we believe that a proper planning is a key to success in this regard.
Ujjwal handles crucial roles like AGM Marketing, researcher, and is an author for KDDL – Eigen. He currently works with Eigen for implementing proven techniques and strategies for marketing plans on online and offline platforms. An expert in efficiently executing SEO, SEM, email marketing, social media marketing, PR marketing, Print campaigns, etc. Ujjwal has coordinated an efficient marketing team on various creative campaigns and programmatic buying to support various digital cross-promotion efforts. Implement efficient search optimization strategies with the help of collateral material and metrics.
In his former years, Ujjwal has years of experience in a managerial role for several reputed companies. His years of experience combined with the flair of writing help him come up with result oriented strategies for Eigen.