Key Benefits of Working with a Stamped Metal Parts Manufacturer
- Design and Engineering |
- Jun 25, 2019
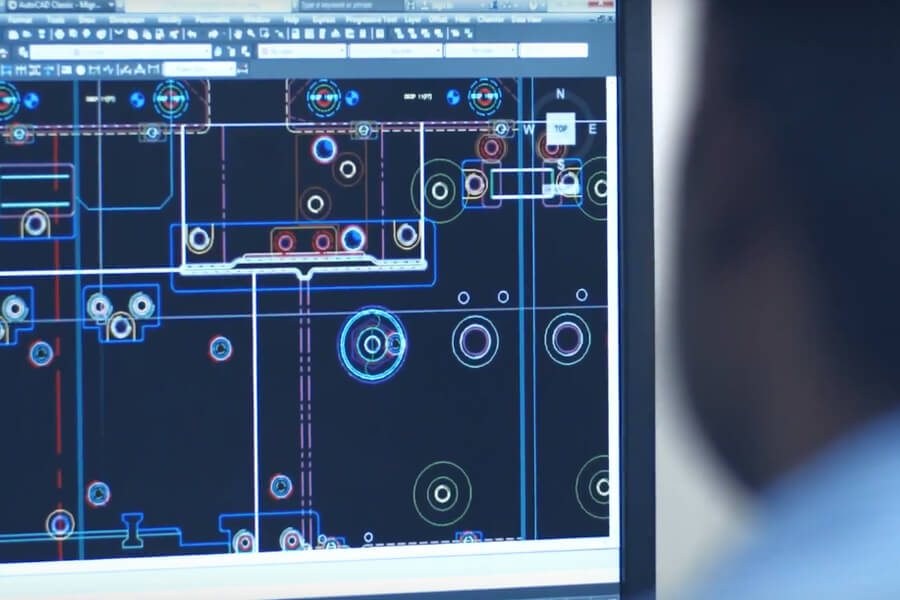
In manufacturing, quality is often quantified in terms of low variation and zero defects. A stamped metal parts manufacturer will only deliver lasting value as a supplier when the client cooperates and works together with them right from the beginning. Here are a few initial steps where your collaboration with stamped metal parts manufacturer could benefit you greatly in terms of money and time.
Data management and Process planning
Metal Stamping process development is an extremely collaborative activity between the stamped metal parts manufacturer and the industry, requiring effective communication between multiple stages including manufacturing engineering, tooling design, product design, industrial operations, and production teams.
An efficient stamped metal parts manufacturer would be able to provide data management, process planning, configuration control, and flexible reporting, in order to ensure the availability of the right data, where and when it is required.
Boost productivity and Reduce cost
Your industry can attain significant gains in cost reduction and manufacturing productivity by using industry best practices and communicating well with your stamped metal parts manufacturer to reduce errors and rework.
Manage complexity
You can manage the data and processes associated with the stamping die design through commissioning process chain. A good sheet metal stamping manufacturer will enable you to leverage product change, dependencies, and updates throughout the development process, resulting in shortened time to production and improved quality.
It is not uncommon for part designs to change often and even late in the development cycle due to evolving engineering, design, and manufacturing requirements. To generate and edit complicated parts quickly and effectively your sheet metal stamping manufacturer might have the necessary tools, but you need to speak what is in your mind. This will enable creative flexibility and maximum efficiency. This way they can easily update models to design changes.
Advantages of working with your sheet metal stamping manufacturer are, Automate checking of part designs which are in conformance to corporate standards, work easily with data from any CAD system by means of data geometry healing, quality checks, and an extensive set of data translators, ensuring proper manufacturability right from the design phase with comprehensive checks for draw, pierce, trim, and flange criteria.
During the early planning phases, when die lineup and production throughput targets are determined the ROI of a press line is established. All critical factors such as die lineup spacing, opening height, and material travel speed can directly influence the frequency of maintenance interruptions and downtime and impact the overall efficiency of the press line.
Together you can generate process model for each station of the press line, and also determine which areas of the part need forming, flanging and trimming. In addition, you can decide on the location of the holes and tip the part into the metal stamping die position.
Optimization of die lineup efficiency
Working together with your stamped metal parts manufacturer can help them calculate part transfer application and speeds, and identify and correct issues caused by part transfer acceleration and speed. Defining clearance zones under production conditions aid in die design and transfer program. Advantages of collaborative work with the sheet metal dies manufacturer are that you would then have optimized the stamping position of parts, accuracy in collision detection, besides other aspects.
Die face design
Ever increasing material prices and operational costs tremendously increase the cost of physical try-outs. If you want stamped metal parts manufacturer to accurately produce desired stamping results with a minimum number of physical try-outs and prototypes then let them know in advance, with absolute clarity, the design you are aiming to attain.
Die structure design and validation
Due to their complexity and due to a large number of components, die assemblies can be time-consuming and tedious to design. These same characteristics that can make it difficult to achieve proper results during the initial try-out. Therefore clearly state what you would want to your sheet metal die manufacturer and the engineers. By improving functional efficiency and by identifying and correcting cam drive malfunctions, stamped metal part manufacturer can extend the life of the die. Advantages of working together at this stage would mean that one can quickly analyze multiple design configurations that are associative to the die design, speed die structure design, save time because one can capture and re-use proven die structure designs for future projects.
Therefore, working with the stamped metal parts manufacturer can quicken the process of metal stamping and reduce the cost of manufacturing the desired components.
Ujjwal handles crucial roles like AGM Marketing, researcher, and is an author for KDDL – Eigen. He currently works with Eigen for implementing proven techniques and strategies for marketing plans on online and offline platforms. An expert in efficiently executing SEO, SEM, email marketing, social media marketing, PR marketing, Print campaigns, etc. Ujjwal has coordinated an efficient marketing team on various creative campaigns and programmatic buying to support various digital cross-promotion efforts. Implement efficient search optimization strategies with the help of collateral material and metrics.
In his former years, Ujjwal has years of experience in a managerial role for several reputed companies. His years of experience combined with the flair of writing help him come up with result oriented strategies for Eigen.