Know about Metal Stamping Suppliers Role in Precision Stampings
- Precision Metal Stamping |
- May 27, 2019
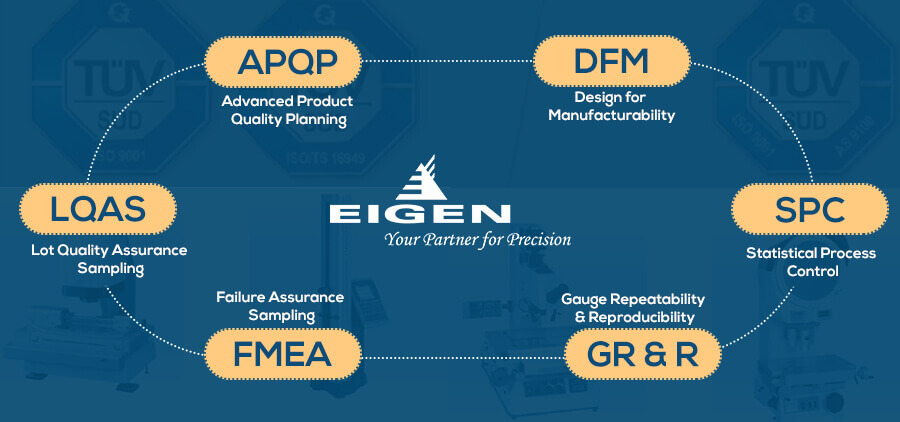
The world has never been as consumer-oriented as it is today. With consumerism constantly on the rise production has a struggle keeping up. This is where precision metal stampings comes in. Metal stamping manufacturers have a key role to play in ensuring that products or components are available in sufficient quantity and are of good quality to satisfy market needs.
What is precision metal stampings?
Precision metal stamping refers to the process of producing metal components or items using a press machine. Punch and die are used to form the item or component from sheet metal. Quality control steps ensure that there are tight tolerances and very negligible variations to ensure that it is a ‘precision’ job. This might sound easy but it is an art to be able to achieve the desired results while ensuring optimum usage of resources and minimal wastage in scrap. Metal stamping suppliers play a key role in accomplishing all this.
What are metal stamping suppliers?
The metal stamping suppliers required vary greatly depending on the project and the end product that is required. The supplier requires a clear and pervasive knowledge of the metalworking industry and must understand the needs of the customer. This then helps him plan and prepare for the job at hand. The punch and die are key components of the process. They are what determine the quality of the end product. These tools and dies are required to perform piercing, blanking, bending, shallow drawing, coining, forming, and progressive processes in the precision metal stamping process.
Metal stamping suppliers can process parts that are made of stainless steel, galvanized steel, cold/hot rolled steel, aluminum, high and low carbon steel, high strength low alloy, brass and copper. Metal stamping suppliers are also performs for secondary operations such as machining, finishing, and assembly processes.
The Punch and Die
The punch and die are the most important elements of metal stampings. High quality and extremely accurate parts with minimal tolerance for error require extremely accurate punch and die tools. For the production of intricate and complex components, metal stamping manufacturers rely on dies made of the highest quality tool sheets and pre-hardened metals.
Many organizations implement an advanced in-die sensor technology in each die that they build. This helps protect the valuable investment that has been made in preparing the die. Then the computerized press control system links with the in-die sensor and thus constantly monitors the precision stampings process. This ensures that the die is protected, and warns of problems before damages occur that could be very cost intensive to rectify. They also allow the press machines to function at their optimum speeds thus speeding up production. The precision metal stamping process is thus able to produce complex shapes and intricate designs for a wide range of components.
Incorporating secondary operations into progressive dies is one way to reduce costs for metal stamping manufacturers. Being able to weld, tap holes, assemble parts and make measurements during the precision stampings process ensures that the workflow is better controlled and streamlined.
Metal stamping suppliers for quality control
Metal stamping manufacturers use a number of tools to ensure that quality is maintained in precision metal stamping. These industry standard tools and gauges help obtain precise measurements. They require regular calibration to ensure that they remain accurate. The importance of accuracy cannot be overstated in the precision metal stamping industry.
As examples of the precision tools required, consider the coordinated measurement machine. This has probes that can reach multiple points in complex parts, locations that are unreachable to the human hand. Or consider the Faro Arm that has extremely accurate lasers able to scan 560,000 points per second. A component’s layout can thus be quickly and precisely defined and this speeds up work without compromising quality or details. Mistakes or deviations can thus be corrected and rectified.
“The quality of work done depends on the type of tools used.” This adage is absolutely true in the precision metal stamping industry. The items or components produced by a metal stamping manufacturer will depend almost totally on the punch and die tools he has used. If they are of the highest quality, we can expect the products to reflect the same high quality. Therefore, choose your metal stamping suppliers carefully.
Ujjwal handles crucial roles like AGM Marketing, researcher, and is an author for KDDL – Eigen. He currently works with Eigen for implementing proven techniques and strategies for marketing plans on online and offline platforms. An expert in efficiently executing SEO, SEM, email marketing, social media marketing, PR marketing, Print campaigns, etc. Ujjwal has coordinated an efficient marketing team on various creative campaigns and programmatic buying to support various digital cross-promotion efforts. Implement efficient search optimization strategies with the help of collateral material and metrics.
In his former years, Ujjwal has years of experience in a managerial role for several reputed companies. His years of experience combined with the flair of writing help him come up with result oriented strategies for Eigen.