Successful Formula for a Sheet Metal Punch and Die
- Design and Engineering |
- May 16, 2019
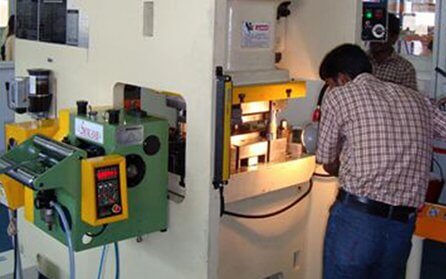
Every company is looking to achieve great success, but in the metal stamping industry it depends on taking several small but meticulous steps rather than taking one giant leap. This principle is very important when the goal is to achieve success in metal punch and die process. By taking small but appropriate steps,the punch and die manufacturers can surely attain increased profitability and productivity. It is crucial then to analyze the overall process and get to know the successful formula to reap benefits in the long run.
Punch and Die Design
Punch and die design can be divided into four important parts:
- Punch
- Die
- Stripper
- And tool holder system.
The success of sheet metal stamping mostly depends upon how efficiently the punch and die manufacturer works with these components.
The Punch
The punch faces both tensile and comprehensive forces during the punching process. When the punch makes contact with the base of the sheet metal under process, it applies the set pressure until it gains the required results. As the punch reaches base of the single stroke, it starts to draw back from the sheet metal. And while the punch moves back to upward position it scrapes the flanks of the punch and applies significant tensile strength to the material.
The secret to alleviate the effects of these inevitable force is to have an appropriate process and successfully design the punch and die.
The Stripper
During the sheet metal punch and die process, there are two important functions that stripper performs:
- Firstly, it holds the sheet metal against die when the punch completes the approach, penetration and retraction cycle.
- Secondly, it tightly grips the tip of the punch as the hole is being punched.
The Die
Unless the punch and die have the right fit, it is impossible to punch a hole successfully. In this regard, the precise alignment of punch and die makes sure that it enters the die and does not make any contact. Here it is important to remember another vital difference between the dimensions in punch and die, which is called the die clearance. Consistent and precise clearance of the die around the punch’s periphery is vital especially when working with square and rectangular tools that have sharp edges. In order to maintain a consistent and precise clearance, the small radius in the corners of the die proves to be helpful.
The Toolholder System
While holding the workpiece against the die’s upper surface, the toolholder systems lead the tip of the punch to the die’s center. Toolholding systems have precise external and internal features that makes it possible to dispense orientation, concentric alignment, and the punch tip’s angular alignment that is relative to the x-y-z punch press axes. Additionally, even at high speeds of operation these are efficient enough to provide stripping. Guided and unguided designs are two distinct tooling systems. An efficient guided system makes it possible to produce top quality components with longer intervals. These also help the components manufactured to be long lasting.
Die Clearance
One of the most important contributions towards the success of the punch and die process is efficient optimizing the die clearance. This helps improve the life of the tool and edge quality and also reduces the overall cost. It may seem like a complex process, but once you get a clear understanding about the complex punching procedure it will be easy to achieve the precise die clearance. Another important thing to remember is to have correct clearance aids when connecting the lower and upper fractures as it helps to free the slug, release the punching force, and helps in the smooth discharge of slug with minimum force and added efficiency.
Slug Diagnosis
Look at the slugs to get an idea about the overall efficiency of your punch and die operation. As slug is the hole’s mirror image, it will help you diagnose if the appropriate clearance is achieved for the operation. The polished land and fracture plane will remain consistent around the slug if the die and machine are properly aligned. If you see that the polished land is not even, look at the tool because in most cases it may not be aligned appropriately. If the slug is good then the punch and die operation will take place in maximum efficiency. It also means that there is maximum interval between regrinds and the cost of sheet metal punch and die is minimized.
Last but not least is to ensure simple maintenance is done at regular intervals. Proper punch and die maintenance include on-time lubrication based on the recommendation of punch and die manufacturers. Manufacturers ensure to use grinding equipment specially designed for sharpening the punch press and this also makes sure that alignment of turret is appropriate.
Ujjwal handles crucial roles like AGM Marketing, researcher, and is an author for KDDL – Eigen. He currently works with Eigen for implementing proven techniques and strategies for marketing plans on online and offline platforms. An expert in efficiently executing SEO, SEM, email marketing, social media marketing, PR marketing, Print campaigns, etc. Ujjwal has coordinated an efficient marketing team on various creative campaigns and programmatic buying to support various digital cross-promotion efforts. Implement efficient search optimization strategies with the help of collateral material and metrics.
In his former years, Ujjwal has years of experience in a managerial role for several reputed companies. His years of experience combined with the flair of writing help him come up with result oriented strategies for Eigen.