Significance of Custom Metal Stamping in the Medical Sector
- Metal Stamping |
- Jan 31, 2023
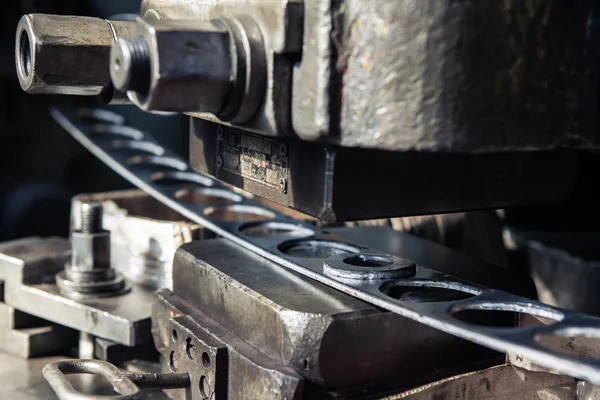
Metal components are now an integral part of medical devices that aid the stimulation and treatment of various diseases through surgical equipment. The main challenge in manufacturing such equipment is to maintain the precision and quality of each of its metal parts.
This is where metal stamping comes into the picture. This metal fabrication method is one of the cost-effective means to create customized metal parts with high accuracy. This article covers all the basic information about custom metal stamping and its benefits for the medical industry.
What is custom metal stamping?
Custom metal stamping is a metal part manufacturing process that accommodates projects with a variety of metal materials to create customized metal parts. It requires custom tools and techniques so the manufacturer designs the metal stamping dies and plans out the process to produce metal parts as per the customer’s design guidelines.
Here a metal sheet goes through a series of metal stamping operations like blanking, drawing, piercing, coining, etc. These metal forming and cutting processes are sequenced in a way that the result matches the design.
Progressive die tooling for medical device custom metal stamps
Metal stamps in the medical industry revolve around the accuracy of the design. These metal parts are usually either small or medium in size, manufacturers prefer progressive die tooling for faster and more precise output. Therefore, progressive die tooling, also known as a cut-carry die, is the best option to manufacture custom metal stamping in bulk for medical devices.
Progressive dies have a series of metal operations lined up in a sequence that depends upon the design requirements. This tooling method performs more than one metal stamping operation at different stages. Therefore, as the metal sheet advances through each of these stations, it gets shaped into the desired design in one go.
Common Custom metal stamps in the medical industry
Metal stamping manufacturers utilize the best tooling like progressive die tooling to create minuscule, complex shapes with tight tolerances.
The custom metal stampings are an affordable means for quality medical device components such as:
1. Surgical Tools and Instruments
Surgical tools and instruments are the most common metal stamped pieces of equipment that need customized design specifications. For example, laparoscopic surgery requires cylindrical jaw housings with certain specifications in terms of thickness and shape. Other commonly used custom metal-stamped surgical devices are forceps, cannulas, and retractors.
2. Medical Devices Covers
For devices that go inside the body, the material selection plays a crucial role as it must be hypoallergenic and resistant to corrosion and bacterial growth. The most preferred material for custom stamped metal parts for implantation is Titanium which is used as enclosures to shield implantable devices like cochlear, pacemakers, drug pumps, etc.
3. Implantable Components
Components like brackets, clips, and battery cases for hearing aids and pacemakers are small as a fingernail clipping. Regardless of being tiny, these components need to have sharp accuracy to design to perform well for a longer period. Therefore, manufacturers prefer precision tooling for the custom metal stamping process.
Steps to ensure successful custom metal stamping for the medical industry
The medical industry requires specific metal components that are cost-effective and high in accuracy. There are some key elements that manufacturers consider to ensure high-quality custom metal stampings apt for medical devices.
Here are some of the crucial points that ensure desired performance and durability of custom metal stamps for medical devices that account for high accuracy and quality:
Step 1 – Making the most of prototyping
Creating prototypes helps designers and developers to understand whether the design works or needs more changes.
Prototypes help them to spot potential issues before investing in high-volume metal stamped parts. It also aids in testing several iterations and finding room for improvement until the design matches the customer’s specifications.
Step 2- Eliminating Secondary operations wherever possible
Medical devices are always in demand, and delivery time is critical factor.
Secondary operations like machining take extra time and labor during production, that indirectly increases the delivery time of the custom metal stamps.
To avoid this, manufacturers make the best of the design stage and simplify the design to ensure on-time delivery without compromising on quality and accuracy.
Step 3 – Partnering with expert custom metal stamping companies
Custom metal stamping companies like Eigen have cutting-edge technologies and knowledge about industrial requirements. Investing in such expertise is worth every penny as they ensure complex geometries are created with utmost precision and in the desired time frame.
Step 4 – Adhering to medical device quality control standards
Medical equipment has strict quality criteria. Hence the best manufacturers verify every product and ensure it matches the industry and customer quality specifications.
Ujjwal handles crucial roles like AGM Marketing, researcher, and is an author for KDDL – Eigen. He currently works with Eigen for implementing proven techniques and strategies for marketing plans on online and offline platforms. An expert in efficiently executing SEO, SEM, email marketing, social media marketing, PR marketing, Print campaigns, etc. Ujjwal has coordinated an efficient marketing team on various creative campaigns and programmatic buying to support various digital cross-promotion efforts. Implement efficient search optimization strategies with the help of collateral material and metrics.
In his former years, Ujjwal has years of experience in a managerial role for several reputed companies. His years of experience combined with the flair of writing help him come up with result oriented strategies for Eigen.