Cost-Effective Solutions of Custom Metal Stampings
- Progressive Die Stamping |
- Apr 10, 2024
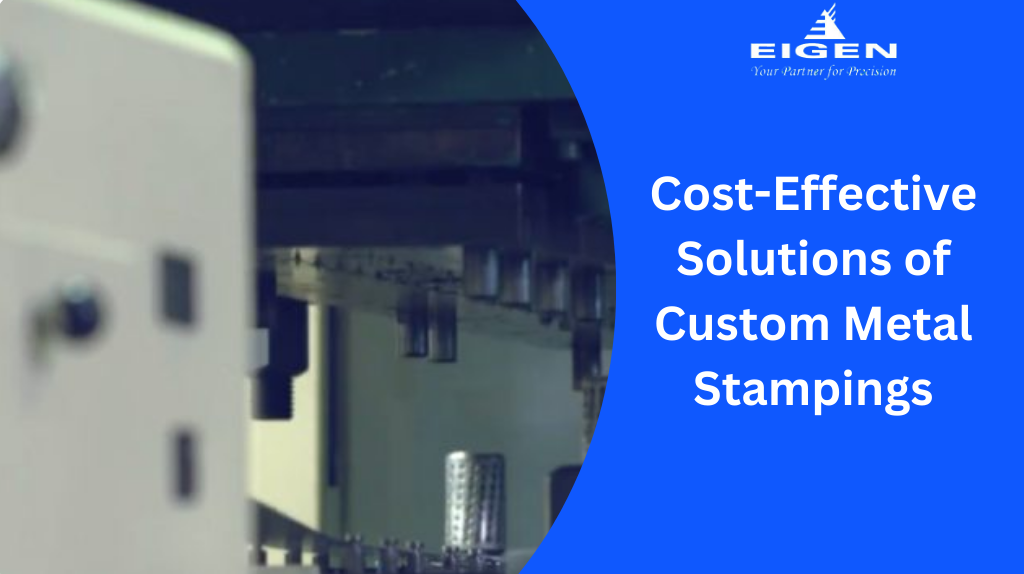
Metal stamping is a vital process in the manufacturing industry. However, like with any industrial technique, expenses can quickly grow, cutting profit margins and potentially damaging quality.
While providing custom metal stamping products, considering the manufacturing cost becomes crucial. Recognizing the importance of cost-cutting in metal stamping is about more than just increasing profits. It also guarantees efficiency, sustainability, and value to the end user.
Are you ready to discuss the details of each method? If you have just started with metal stamping, read this post for insights and subtle details that can transform your metal stamping operations.
Don’t Use Exotic Materials
Using unusual materials for custom design can dramatically raise production costs. These materials are not only expensive to purchase but may also necessitate specialist handling and processing, increasing expenses.
Using the common materials for metal stamping that are widely available has been tried and proven over time. They are dependable, easy to source, and generally less expensive than their exotic cousins.
The choice of the sheet metal stamping process directly impacts the end product’s quality, performance, and even market reception.
Know the Material Market
The materials market is subject to fluctuation. Being proactive and strategic about the price range of the materials can result in significant savings.
Metal prices fluctuate on various variables, including geopolitical events and supply chain disruptions. Keeping an eye on these changes enables organizations to make good purchase decisions.
When you buy a particular material in bulk, then it would save a significant amount. Also, constantly check for price fluctuations and the discounts the branded company offers.
Tooling Efficiency
In metal stamping, tools are the unsung heroes. Using the right metal stamping tool for a certain operation ensures precision, lowers the possibility of errors, and improves overall product quality.
Regular maintenance ensures that tools run smoothly, reducing the likelihood of unexpected problems that can interrupt production. While maintenance is costly, the costs associated with tool breakdowns, replacements, or defective goods can be significantly higher.
Tool optimization is not just about lowering maintenance costs. A metal stamping tool improves production efficiency, reduces waste, and may have a longer operational life. It is a long-term dividend-paying investment.
Automate Process
The development of Industry 4.0 has pushed automation in manufacturing, providing numerous benefits, particularly in processes such as sheet metal stamping.
Automation can minimize the demand for manual labor, particularly for repeated jobs. Modern automated devices frequently use less energy, resulting in lower power bills.
While automation offers efficiency, it requires an upfront investment. Furthermore, over-automation might limit flexibility, making responding to unexpected market shifts or unique demands difficult.
Use the Correct Type of Die
Progressive and transfer dies have both advantages and downsides in terms of cost. With a limited production run, a transfer die is frequently less expensive than a progressive die.
Alternatively, a progressive stamping die design is often appropriate if you need many pieces. For instance, using a progressive die for limited production costs more. So, know the demands and use the correct die type to save money on custom metal stamping.
Relax Tolerances Where Possible
Some engineers become extremely strict in their design standards. Quality is always required to reduce defective products, but exceedingly tight tolerances will raise your tooling costs.
Understand your part and production process; what level of precision is required downstream? Relax your tolerances wherever possible and save money for the most important pieces.
The metal stamping die design should prioritize finding the correct balance between precision and cost-effectiveness, which provides peak performance without incurring needless costs.
Reduce Scrap Metal
Scrap metal refers to sheet metal bits that do not make up the final product. Scrap metal does not go to waste because it can be recycled.
Still, the scrap is less valuable than the sheet metal because it must be recycled. Any scrap metal signifies lost money. Innovative die design will reduce scrap metal and thus allow you to lower your costs significantly.
Consult with Manufacturer
Every successful metal stamping die design manufacturing process relies on the experience of experts who understand production, materials, and tools. Consulting with a manufacturing engineer can have an important effect.
Manufacturing engineers can detect bottlenecks or errors in the production process and suggest remedies. Their knowledge may guide material selection, assuring peak performance without wasting needless costs.
Collaboration with a manufacturing engineer provides a new perspective on the sheet metal stamping process, such as production workflows, material selection, and tool usage. It frequently identifies opportunities or issues that individuals completely immersed in the process may overlook.
Also Read: Progressive Stamping Die Design Tips
Final Words
Metal stamping cost savings are more than just a financial endeavor. They are capable of significantly increasing your return on investment. They provide a commitment to excellence, sustainability, and providing unmatched value.
If you are a professional stamping supplier, you should prioritize efficiency and innovation to reduce manufacturing costs while maintaining the highest levels of quality.
Ujjwal handles crucial roles like AGM Marketing, researcher, and is an author for KDDL – Eigen. He currently works with Eigen for implementing proven techniques and strategies for marketing plans on online and offline platforms. An expert in efficiently executing SEO, SEM, email marketing, social media marketing, PR marketing, Print campaigns, etc. Ujjwal has coordinated an efficient marketing team on various creative campaigns and programmatic buying to support various digital cross-promotion efforts. Implement efficient search optimization strategies with the help of collateral material and metrics.
In his former years, Ujjwal has years of experience in a managerial role for several reputed companies. His years of experience combined with the flair of writing help him come up with result oriented strategies for Eigen.