How to Utilize Metal Stamping Die Design to Reach Ultimate Objectives
- Design and Engineering, Metal Stamping |
- Mar 12, 2024
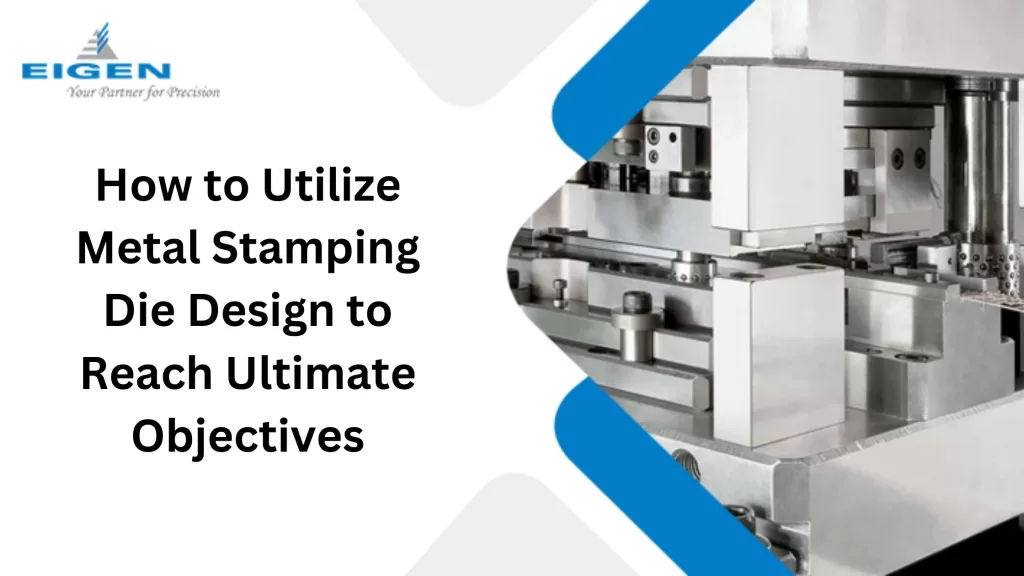
Metal stamping is an adaptable, efficient, and unique manufacturing technique. This system involves reworking flat metallic sheets or coils into complex shapes using a stamping press and specialized tooling.
Metal stamped components carry out critical roles in a huge variety of industries, together with automobile, electrical, aerospace, and alternative energy.
Given its extensive range of applications, gaining intensive expertise in the metal stamping die design process is critical. Here are the steps inside the metal stamping procedure to perfect the layout.
Preparing for Metal Stamped Components
Before beginning the production of metal stamped process, manufacturers and clients should go through a sequence of important tactics. It is to ensure that the finished product meets expectations.
Know the stamping types
Metal stamping presents several methods for generating top finished products. Progressive die stamping, which makes use of a nonstop method to shape metal sheets successfully, is one of the key categories. Deep Draw Stamping creates complex, deep drawn parts by pushing metal sheets into dies.
Fourslide Stamping, which uses horizontal slides, creates complicated bends and forms. Each process is tailored to individual manufacturing necessities. It demonstrates the range and flexibility of metallic stamping in accomplishing precision and performance.
Material Considerations
Selecting the correct materials for the metal stamping die design is vital to making sure longevity, precision, and standard effectiveness. Hardness, thermal conductivity, and wear resistance are all critical factors to remember when deciding on stamping materials.
Optimal material choice contributes to the durability of the die. It makes sure its performance at throughout time and increases the overall efficiency of the metallic stamping procedure. A complete examination of those material factors is required for consistent and the best effects in metal stamping.
Tooling Considerations
Tooling has to be carefully considered to ensure an efficient, specific, and a success metal stamping.
Choosing the proper tools requires selecting appropriate dies for the task and working closely with design engineers to validate the desired method at some stage in the prototype phase. This guarantees that the equipment used align absolutely with the task’s necessities.
Tolerance and Accuracy
In metal stamping, achieving precise tolerances is vital for meeting strict design standards. To produce consistently exact stamped parts, the die design must consider variables such as material thickness, temperature changes, and external effects.
Understanding and accommodating these differences throughout the design process is critical. It is to ensure the integrity and adherence to requirements throughout the metal stamping production cycle.
Simulation and Prototyping
Using modern tools and prototyping approaches is an important strategy for achieving precision and consistency in the metal stamping process. Designers obtain significant insights into potential concerns by subjecting die designs to virtual simulations and constructing physical prototypes before full scale production begins.
This proactive approach improves the die design and considerably minimizes the possibility of problems. Minimizing the need for costly adjustments during production saves resources and assures a smoother and more efficient metal stamping process, thus improve. This improves the overall quality of stamped parts.
Precision in Every Cut
Metal stamping, which goes beyond conventional blanking, encompasses a variety of precision procedures. Beginning with blank creation, wherein steel sheets assume form, the next levels encompass piercing, bending, coining, and modern die stamping. Precision is important at each degree.
Punching, shaping, and embossing tactics improve components to ensure structural integrity and aesthetic attraction. This adaptable production generation organizes a specific movement, reworking raw metal into intricately sculpted parts. In metal stamping, every cut demonstrates the accuracy and engineering finesse that combine to reap excellence.
Also Read: The Crucial Role of Metal Stamping in Precision Components for Aerospace
Die Configurations
The optimization of stamping die configurations is critical in increasing production speed. Notably, progressive die designs provide a strategic advantage by allowing numerous operations in a single pass.
This streamlined technique reduces downtime, leading to a significant boost in overall throughput. Manufacturers can increase the efficiency of their metal stamping process by properly setting the die.
Integration of Automation
Integrating automation functions in the die layout emerges as a transformative strategy for reinforcing productiveness. Automated systems, together with feeding mechanisms, ejection structures, and satisfactory manipulate strategies, are pivotal in decreasing manual intervention.
This reduction leads to best results in higher performance. Also, it reduces labor charges. The seamless integration of automation into die design quickens the steel stamping system and ends in affordable and efficient manufacturing workflow.
Safety Measures
Manufacturers play a vital function in ensuring the safety of metal stamping components. It is vital to use equipment designed particularly to remove burrs and smooth sharp edges.
This improves the completed product’s safety and also facilitates produce final parts that fulfill the exceptional requirements.
Final words
By following steps, manufacturers can enhance the complete production technique’s performance, precision, and protection. It guarantees the delivery of the exceptional stamped components that meet expectations. Look for a professional stamping supplier who makes use of modern techniques to obtain the final goals in metal stamping.
Ujjwal handles crucial roles like AGM Marketing, researcher, and is an author for KDDL – Eigen. He currently works with Eigen for implementing proven techniques and strategies for marketing plans on online and offline platforms. An expert in efficiently executing SEO, SEM, email marketing, social media marketing, PR marketing, Print campaigns, etc. Ujjwal has coordinated an efficient marketing team on various creative campaigns and programmatic buying to support various digital cross-promotion efforts. Implement efficient search optimization strategies with the help of collateral material and metrics.
In his former years, Ujjwal has years of experience in a managerial role for several reputed companies. His years of experience combined with the flair of writing help him come up with result oriented strategies for Eigen.