What Is Metal Stamping And What Are Its Design Principles?
- Metal Stamping |
- Jan 2, 2023
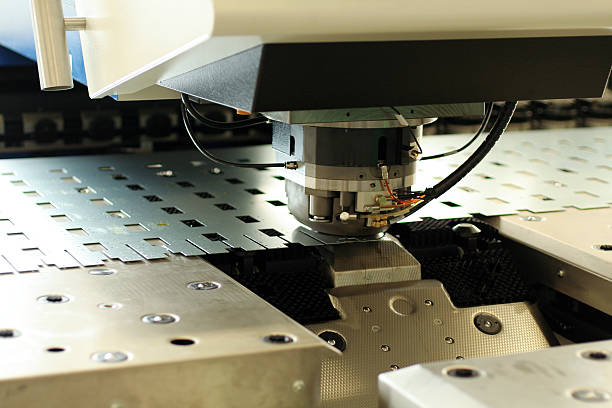
The average individual may not realize it, but metal stamping is a vital aspect of the production process. It gives numerous benefits to different industries and businesses all over the world. Metal stamping is a simple yet versatile production technology. Innovators have refined and enhanced it throughout time to produce the incredibly efficient methods now employed. Metal stamping is a low-cost, high-speed stamping manufacturing method that produces many identical metal components. With that in mind, here’s more information about metal stamping and how it works.
What Exactly Is Metal Stamping?
Metal stamping is an industrial method used to shape flat metal sheets. It is a complicated procedure that can involve a variety of metal-forming processes.
Stamping is inserting flat sheet metal into a stamping press. It can either be in coil or blank form. A tool and die surface molds the metal into the required shape in the press. Stamping techniques used to form metal include:
- Embossing
- Punching
- Bending
- Blanking
- Flanging
- Coining
Discover Automotive Metal Stamping Process
How Does Metal Stamping Work?
Metal stamping transforms a flat piece of metal into a specific and desired shape. It is a sophisticated operation that entails multiple complicated and intricate steps. Nevertheless, metal stamping is essential to generating inexpensive and well-crafted parts and components in various industries. These industries range from automotive and aerospace to medical and electronics.
Metal punching is a fabrication method where the punch enters the punching die and extracts a scrap slug from the workpiece. Punched material is often in sheets, however, rolled metals are also applicable. The procedure creates a hole in the die that is exactly the size of the pattern. This method accurately produces holes of various shapes and sizes.
Coining is a metal bending process in which a die and punch press stamps the item between them. This forces the punch point to penetrate the metal, resulting in precise, repeatable bends. In addition, the deep penetration releases internal pressure in the metal plate, resulting in no spring-back effects.
By pressing a sheet against the die in the shape of the desired pattern, embossing creates a raised design. When the metal goes into an embossing machine, a tool raises the other side of the blank. The embossed design has a smooth surface since the blank was on a piece of rubber or foam.
Also Read- Automotive Stamping Dies Save Big With Metal Stamping
Flanging is the technique of placing a flare onto a metal workpiece using the following:
- Dies
- Presses
- Specialist flanging apparatus
Bending is a technique for deforming metal into L, U, or V-shaped profiles. Mechanical, pneumatic, hydraulic, and CNC press braking are the many types.
Principles of metal stamping design
In general, you should avoid overly narrow projections in stamped items. This is because they easily become warped and affect the perception of quality in the finished product. Designs should, whenever possible, stem from using existing dies for common forms and bends. The requirement to design a specialized die for stamping will raise the initial tooling expenses.
You can handle some challenges by creative tool design, while others cannot. For example, some stamping designs satisfy all of the dimensional criteria is nearly impossible. This shoddy design for manufacturability might lead to excessive maintenance and scrap expenses. Production requires constant changes and service, resulting in an extremely inefficient program.
Metal stamping is a cost-effective method of making large quantities of parts with various features. These features include strength, durability, good conducting properties, and stability. Here are some metal stamping design guidelines that can help you create a product that uses all the benefits of the metal stamping process.
1. You must develop metal stamping components to meet product and technical performance requirements.
2. Under typical use conditions, designed metal stamping parts aim to reduce the dimensional accuracy grade and surface roughness grade requirements. It is helpful to:
- Product interchange
- Waste reduction
- Product quality stability
3. The design of stamping components must be conducive to improving the following:
- Use of metal materials
- Reducing the variety and specifications of materials
- Reducing material consumption as much as possible
Allow low-cost materials to be in use as much as possible so that parts do not go to waste and generate less scrap.
4. The design of precision stamping parts must be simple in shape and reasonable in structure. This is to help simplify the mold structure and simplify the number of processes, i.e.,
- The one with the fewest, simplest stamping process to complete the parts processing
- Reduce the use of other processing methods
- Conducive to stamping operation
All this is for the organization of the realization of mechanization and automation of production and to improve labor productivity.
5. The planned metal stamping components should process current equipment, process equipment as feasible, and assist die service life extension.
Also Read- Benefits of Using Combination Die For Your Metal Stamping Project
Stamping designs are quite robust and cost-effective when the product designer consults with the parts manufacturers. When the manufacturing and component design teams collaborate, the result is the optimal production design—and often a component stamping cost savings of up to 50%. A well-thought-out design for manufacturability, thoroughly assessed by both the component design and manufacturing teams, will result in the highest-quality stamped part at the lowest cost. That’s in everyone’s best interests.
Ujjwal handles crucial roles like AGM Marketing, researcher, and is an author for KDDL – Eigen. He currently works with Eigen for implementing proven techniques and strategies for marketing plans on online and offline platforms. An expert in efficiently executing SEO, SEM, email marketing, social media marketing, PR marketing, Print campaigns, etc. Ujjwal has coordinated an efficient marketing team on various creative campaigns and programmatic buying to support various digital cross-promotion efforts. Implement efficient search optimization strategies with the help of collateral material and metrics.
In his former years, Ujjwal has years of experience in a managerial role for several reputed companies. His years of experience combined with the flair of writing help him come up with result oriented strategies for Eigen.