Stamping Die Parts- an Integral Part of Sheet Metal Forming
- Design and Engineering |
- Mar 12, 2020
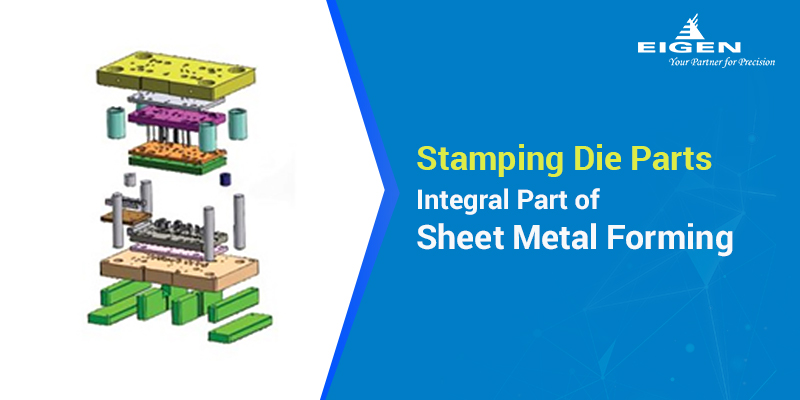
Sheet metal forming is an age-old process that dates back to 5000 B.C according to historical sources. It is a method that is employed to produce all kinds of shapes and sizes. The output is durable and also lightweight if that’s the requirement. Some of the parts that can be formed with sheet metal forming are cans used for filling beverages, cabinets used for storage of files, various appliances, car bodies, and even metal desks. Sheet Metal forming makes uses of a wide variety of commonly found materials like aluminum, titanium or low-carbon steel. One of the first steps in sheet metal forming is to get a metal sheet into a piece form by cutting it using one of the various methods like shearing, cutting, sawing or slitting. Even a coiled sheet can be used to get a metal piece out of it. The piece of metal so formed can then be converted into various shapes by a variety of complex processes. Some of these are blanking, punching, stamping, embossing, bending, forming and deep drawing.
In order to carry out the process of stamping, huge presses are used which are called stamping presses. Three of the most commonly used presses are hydraulic, mechanical and mechanical servo presses. These presses are generally connected to a feeder which automatically sends sheet metal in coil or blank form through the press. Here are some details about each of the stamping presses and stamping die components.
Hydraulic:
in these presses hydraulic fluid is used to apply force on the metal. The amount of pressure applied can be controlled to a very precise degree in this type of press. This makes it possible to apply consistent pressure on the metal to be formed and the result is much more refined than the mechanical press. Another added benefit of these presses is that they offer adjustment options to the speed and stroke functionalities. It is possible to even deliver maximum power during the stroke using this particular method. Also, the options of stroke sizes in this press are varied, from 10-800mm. Typically, hydraulic presses are used for productions that are small and complex since they offer a great amount of control on various aspects of the stamping process.
EXPLORE OUR DESIGN & ENGINEERING SERVICES
Mechanical:
As the name suggests, these presses make use of the mechanical balance wheel to store and relocate forces. A machine motor is connected to the balance wheel which does the job. Different types of mechanical presses can bore different sizes of holes ranging from 5-500mm. Mechanical presses work much faster than hydraulic presses as they can deliver strokes ranging from 20-1500 strokes every minute. Not just that, these presses are also available in a variety of sizes, both large and small. The typical usage of these presses is to produce simple parts that are shallow and bored out of sheet metal which is coiled. Mechanical presses are widely used for transfer and progressive stamping during huge productions.
Mechanical Servo:
The difference in these presses is that instead of a balance wheel, motors with high capacities are used. These presses can produce intricate stampings at a much faster rate than the hydraulic presses. Like the hydraulic press, this one also offers a wide range of control in various aspects of the stamping process. Everything from speed, movement and position of the slide and stroke can be fully controlled. Dive systems are used to power these presses, both direct drive and link assisted ones. With so much flexibility, these presses are the costliest of the three.
Stamping dies also come in different types. Typically, they are either single or multi-station. A single station die includes combination and compound dies. As the name suggests, compound dies are used to create multiple cutting processes within a single press. These are widely used in the production of steel washers which need various cuts. Multi-station dies to include progressive and transfer dies in it. The reason for employing these two dies is to facilitate multiple operations like cutting, notching and punching using the same set of dies. There is also the possibility of using combination dies which can carry out cutting and non-cutting operations in a single stroke. These are used where cuts and rims are to be carved in the same metal piece. Knife dies or steel rule dies are used to cut and shape metals like copper, brass, and aluminum. There is a steel strip that is used to cut the surface which matches the shape that needs to be carved; a hole in the die shoe holds the steel material together.
Stamping Dies consist of several parts or stamping die components like bushings, die pins, die plates, shoes, heel blocks, heel plates, die sets, guide pins, dowels, screws and keys. There are some other stamping die components that are vital like drawing pads, pressure and stripper. These stamping die components need to be secured using keepers, shoulder bolts, retainers, spools, springs, coil and also gas.
Here is a brief description of these stamping die components.
Die sets, die plates and shoes- These are made out of aluminum or steel and match the size of the die. These three together form the foundation of working stamping die parts. These components of the stamping die need to be milled or ground so that they remain flat and are parallel. Aluminum is a great choice for these stamping die parts as it is lightweight, can be machined fast and is more durable. The stamping die set is made out of an assembly of upper and lower die shoes, fastened with die pins. As far as the thickness of the stamping die shoe is concerned, this is determined depending on how much pressure is expected during the cutting and carving process.
EXPLORE OUR DESIGN & ENGINEERING SERVICES
Bushings and Guide Pins:
These both help keep the upper and lower stamping die shoes in alignment. These are tiny in size and are essential of two types, either bearing style pins or friction pins. These pins are made out of hardened steel while the bushings are made from aluminum-bronze material. These pins are advantageous as they help reduce friction and allow for separation of the upper and lower stamping die shoes.
Heel Plates and Blocks:
Heel blocks are made out of steel and fixed to the upper and lower stamping die shoes. The wear plates within them help absorb any side pressure that may be generated during the cutting and carving process. Force-directed from a single direction could cause the guide pins to deflect and create chances of improper alignment in the process and hence these blocks are essential.
Keys, Dowels and Screws:
arts of the upper and lower die shoes are fastened using screws. Dowels help fix die shoes into their assigned place. Keys are made out of steel and help in locating die sections and its parts.
At Eigen, we master the art of metal stamping each time it is done. Our manufacturing plant has state of the art technology and our engineers are the best in the field with years of practical experience. They are also extremely professional and knowledgeable in their field. A number of challenging productions have been successfully carried out by our team, challenges are now their favorites. Depend on us for your stamping needs, we will deliver you nothing but the best.
Ujjwal handles crucial roles like AGM Marketing, researcher, and is an author for KDDL – Eigen. He currently works with Eigen for implementing proven techniques and strategies for marketing plans on online and offline platforms. An expert in efficiently executing SEO, SEM, email marketing, social media marketing, PR marketing, Print campaigns, etc. Ujjwal has coordinated an efficient marketing team on various creative campaigns and programmatic buying to support various digital cross-promotion efforts. Implement efficient search optimization strategies with the help of collateral material and metrics.
In his former years, Ujjwal has years of experience in a managerial role for several reputed companies. His years of experience combined with the flair of writing help him come up with result oriented strategies for Eigen.