Progressive Stamping Tool Concerns For the Metal Stamping Industry
- Progressive Tooling |
- Apr 25, 2019
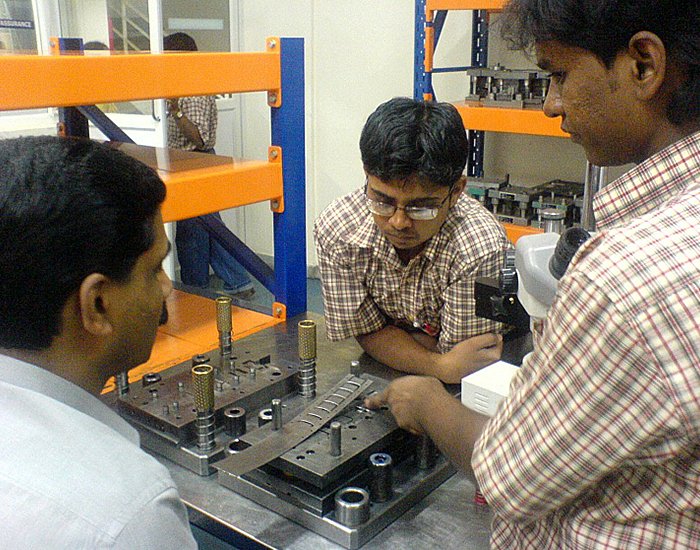
In any metal stamping tool operation, trial and error method is not considered to be a practical approach to find the source of a problem. Time and money is also saved when in-depth analysis and research is done in the initial stage when compared to doing at the end. It is crucial to prevent the problems from occurring after the dies have been built and operations start. In order to accomplish this, the progressive stamping tool and die engineers, operators, designers, and production managers now have advanced tools and technology to help them make changes on the “easy side of the press.”
Certain errors cannot be detected by the naked human eye or might be even dangerous if you have to take a closer look. It might need cameras which is safe, and that can capture images in close proximity. Too many problems occur because material is out of spec, or because of the work material’s metallurgy.
Every progressive stamping tool stroke deploys the right amount of pressure on the raw material. However, there could be serious issues if the sensors are not in the right place. If not taken care of the metal feeding can be messed up, it may not discharge correctly, and the part or die can further be damaged. In turn, this can have an impact on the final production and parts can be wasted, increase material waste, damaging the tooling, delay production, and increase the overall costs. Press tool manufacturers are turning to new metal stamping sensor technology to rectify problems before they cause massive losses. The professional industries are making best use of this advanced technology rather than relying on traditional ways to do it.
Metal stamping sensors are the in-thing of metal stamping industry
Metal stamping industries use several effective techniques to look for defects and immediately address any quality issues. On the other hand, there are certain limitations with the mechanical technology. As an example, micro-switches and electric pilots used on progressive stamping tools are effective in detecting the locations of the raw material inside the stamping tooling machine and easily check for misfeeds. However, these are not designed to stop the metal stamping tools, and this could further give way to damaging the tooling, the component and also the press.
Also Read: What You Need to Know About Progressive Die Stamping
High reject rates, die crashes, cosmetic defects on parts, high levels of scrap and so on, are indicators that the manufacturers need to replace out-of-date monitoring techniques and tools with the latest sensor technology specifically designed to be used in the metal stamping industry. These issues with the progressive stamping tool runs affect the metal stamper and also the client is negatively affected by the expense of rebuilding or repairing a metal stamping tool or line interruptions.
EXPLORE OUR PROGRESSIVE TOOLING SERVICES
The modern metal stamping sensor technology is efficient in addressing the most annoying problem metal stampers face, and this is way before serious damages are caused. In this regard, if the sensors are not functioning it will have an impact on the press operations. The benefits of press tamping tool sensors are:
- Zero defects and improvement in quality,
- Cost of sorting is reduced
- Delivery timing is improved
- Improvement on the focus root cause
- Reduction in the maintenance cost of tools
- Down time and setup time reduction
How do electronic in-die sensors work?
The metal stamping process is more complex than it may seem. With each progressive stamping tool and process, the in-die sensors need to be programmed and customized. Depending upon the project and type of metal being stamped, the electronic sensors will need to be customized accordingly. There is a perfect set of settings that is required and these need to be used in the right harmony with the progressive stamping tool controls. These need to be efficient enough to automatically turn off the system before the die crashes.
Also Read: Precision Tooling Vs. Super Precision Tooling: Difference Explained
Testing progressive stamping tool sensors to ensure accuracy
The sensors need regular testing to ensure that they operate efficiently. It is important to remember that the integrity of both the stamping tool and sensors is at the stake. The metal stampers meticulously check all sensors to closely monitor every sensor’s accuracy and consistency. This process also helps them ensure that the sensors will operate well in the frequent shock of operations in progressive stamping tool.
DISCUSS YOUR PROGRESSIVE TOOLING NEEDS? CONTACT US!
Sensor technology is enabling metal stampers to produce extremely intricate parts without a malfunction. And sensors are capable of measuring critical angles and features on each and every part that goes through the press. Therefore, while putting a stop to die crashes and minimizing downtime, metal stampers are able to ensure part quality.
Ujjwal handles crucial roles like AGM Marketing, researcher, and is an author for KDDL – Eigen. He currently works with Eigen for implementing proven techniques and strategies for marketing plans on online and offline platforms. An expert in efficiently executing SEO, SEM, email marketing, social media marketing, PR marketing, Print campaigns, etc. Ujjwal has coordinated an efficient marketing team on various creative campaigns and programmatic buying to support various digital cross-promotion efforts. Implement efficient search optimization strategies with the help of collateral material and metrics.
In his former years, Ujjwal has years of experience in a managerial role for several reputed companies. His years of experience combined with the flair of writing help him come up with result oriented strategies for Eigen.