Basic Difference Between Progressive Die Stamping Process and Transfer Dies
- Progressive Tooling |
- May 26, 2020
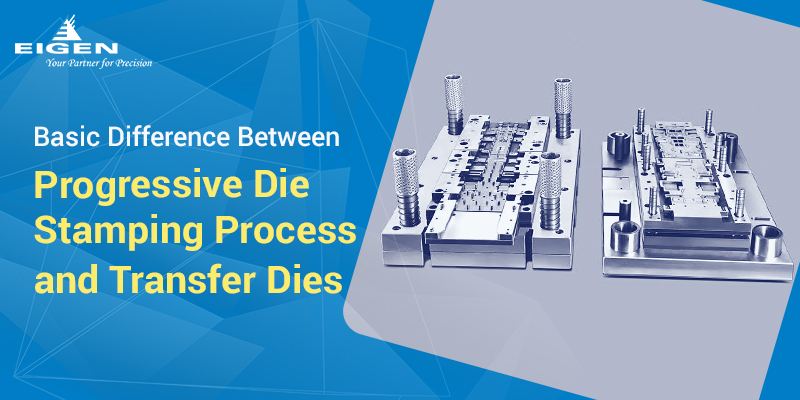
Metal is used in almost everything that we see around us. From household items to heavy industrial equipment, we see metal being used in almost every size and shape. Progressive die stamping process is one of the most commonly opted for by industries to keep up with the increasing requirements. There are different types of dies and processes that are used in the metal stamping industry. If you are planning to delegate a project to a metal stamping manufacturers it is important to understand the differences between the techniques and which one to use for your particular project.
A Little About the Progressive Die Stamping Process
A progressive tool is used in projects wherein the manufacturer is stamping complex or simple parts in large quantities. Metal is fed through the feeding station in coil form and as the name suggests the metal goes through a progressive tool. There are a series of stamping stations that run in the punch press to perform the required operation. The material is precisely uncoiled and straightened throughout the process and then the precise increments are planned throughout the tools to convert the coil into metal stamping. Every workstation is designed to add to the work of the previous station and complete the cycle. Once the material goes through the entire tool, the stamping process is complete.
In progressive die stamping process, it is important to ensure that the metal is precisely fed into each station. This requires a deep understanding of metal stamping, sophisticated technology for the placements of sensors, and the likes. Overall, it is complex to develop progressive metal stamping process. There are a number of complex processes that progressive tooling system can perform such as blanking, lancing, coining, piercing, notching, perforating, embossing, forming, drawing, and so on.
A Little About the Transfer Die Stamping Process
Transfer die stamping is similar to progressive die stamping process, the only difference being that the part if free from metal strip. So instead of designing a system to feed the metal in different stations progressively, this die is designed to manually transfer the strip from one station to the other. In a transfer die, there could be a single die, multiple dies, or a range of dies arranged in a row to form a production line.
The process is fairly easy to understand. In this process, a strip of metal is fed into the first station wherein the blank is cut. Then the blank is transferred through various forming stations mechanically or manually. This die is versatile and so there are a lot of designs possible in the primary operations such as cut-offs, chamfering, knurls, ribs, pierced holes, etc. Some of the processes where transfer dies are preferred are shells, tube applications, frames and structural components, large parts that require transfer among several presses for completion.
EXPLORE OUR PROGRESSIVE TOOLING SERVICES
Key Features and Benefits of Progressive Vs. Transfer Die Stamping
Choosing the appropriate metal stamping technique. The size, production volume, and cost are the primary factors that help to choose a technique that gives optimum results with the highest possible accuracy.
The best way to judge which metal stamping technique is best for your application is to compare its features and benefits. Here’s a quick yet-to-the-point comparison to help you out!
Features & Benefits of Progressive die stamping versus transfer die stamping
PROGRESSIVE DIE STAMPING | TRANSFER DIE STAMPING |
Multiple workstations but Single Die | Single or multiple workstations, and different dies for each |
No lift and shift of metal sheet during the process | Meta sheet is lifted and placed from one workstation to another |
High speed | Slow to moderate stamping speed. |
Produces multiple of the same or different parts from a single die. | Produces different parts from different dies. |
Suitable for small or medium sized parts | Suitable for large sized parts |
Less run-time, as the whole process goes on without any metal sheet transfers | More run-time, as the metal sheet is transferred to different dies for each operation |
Things to Consider When Choosing Between Progressive Tooling and Transfer Die
There are a number of things that you need to consider when choosing between the type of stamping process that you opt for. Here are some of the important things that you should consider:
Progressive Die Stamping
This stamping process is suitable to produce small to large components and is considered to be the most economical to run for large production requirements. It provides faster production speeds and is preferred for stamping projects with tight tolerances. It only requires one set up to produce the parts and in this way helps you save time, money, and a lot of extra settings that are normally required before, during, and after a production run.
Transfer Die Stamping
It is considered to be the best option especially when producing large parts. For shorter production runs, this is one of the most cost-effective approaches. These dies do not need a lifter or sheet guides because these are carried out with independent dies. The single or multiple dies used in this process is beneficial because it comes with a lower tooling cost.
The best stamping process that you choose will mainly depend upon your unique or custom stamping requirements. Every manufacturer is different and the recommendations that come from these professionals will also make a difference in this regard.
Choosing the Progressive Tooling Manufacturer
It is interesting to see all manufacturers promising the best and latest manufacturing techniques. However, the truth is that not all of them have the appropriate tooling, manpower, technology, or even the quality that you are looking for. It is crucial to spend time identifying the best manufacturer that suits your needs and only chooses the one that is best suited. A little research in this regard will go a long way to help you achieve precision and great results at a lower cost as well. The technology curve has shifted in the recent past, and this means that there are a lot of manufacturers that may be playing catch up. Here are some of the important points to help you choose the right manufacturer for your stamping needs:
- Look at the reputation of the manufacturer in the metal stamping industry.
- Carefully consider the kind of clientele that they have and are serving at the moment. This will give you an idea about their expertise.
- Analyze the type of technology that the Progressive die manufacturer is using. The latest technology helps a manufacturer to save a lot of effort, time, and money for the clients.
- ISO certification reflects a lot on the kind of quality that the company has maintained and what you can expect.
- Pay a physical visit to the manufacturing unit if possible to get a clear picture of the quality and type of service to expect from them.
EXPLORE OUR PROGRESSIVE TOOLING SERVICES
The Best Precision Stamping Manufacturer in India
India has many reputed names in the precision stamping industry and Eigen is one such name. With over 15 years of experience in the precision metal stamping industry, Eigen stands out as a preferred choice for customers from across the globe. The manufacturing unit is located in Bangalore, India and has good connectivity with the other countries as it is very close to the airport. Using the latest technology in design and tooling of progressive die stamping, the manufacturer ensures that the clients get the best results at all times.
Ujjwal handles crucial roles like AGM Marketing, researcher, and is an author for KDDL – Eigen. He currently works with Eigen for implementing proven techniques and strategies for marketing plans on online and offline platforms. An expert in efficiently executing SEO, SEM, email marketing, social media marketing, PR marketing, Print campaigns, etc. Ujjwal has coordinated an efficient marketing team on various creative campaigns and programmatic buying to support various digital cross-promotion efforts. Implement efficient search optimization strategies with the help of collateral material and metrics.
In his former years, Ujjwal has years of experience in a managerial role for several reputed companies. His years of experience combined with the flair of writing help him come up with result oriented strategies for Eigen.