Embracing Progressive Die Stamping for High-Volume Manufacturing Demands
- Progressive Die Stamping |
- Feb 2, 2023
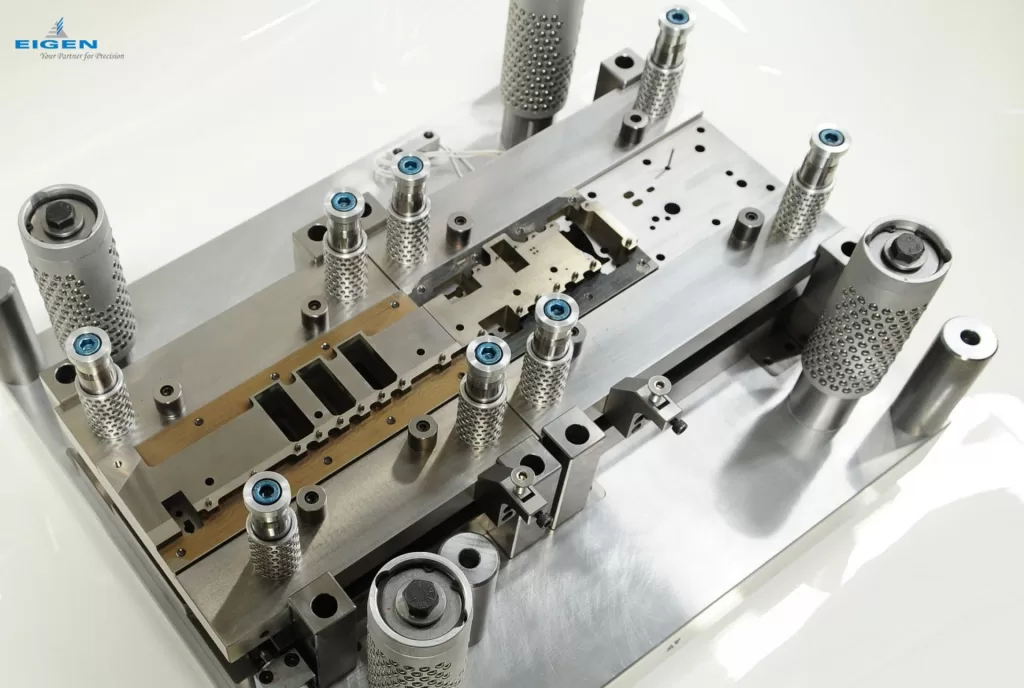
When it comes to manufacturing high volumes of complex metal parts, progressive die stamping is always the first choice of tooling. This metal stamping die is popular for its high performance, especially for high-volume requirements. High volumes could be as many as 1 million parts per year or more.
How does Progressive die stamping for high volume work?
Progressive die stamping parts uses a multi-stage forming tool mounted on a stamping press. The process starts with feeding a metal sheet into the progressive die, where the sequence of different metal stamping operations decide accuracy of the results.
It performs multiple metal operations in one die and a single pass. As the metal strip progresses through the feed, the strip gets subjected to different metal forming and cutting operations. In the end, the metal part gets cut from the strip. The left-out material in the metal strip is called scrap metal. Since progressive metal stamping keeps precision at the highest priority, the metal strip moves and lands within a few 1000th inches. It ensures the proper placement of metal strip in a position where the die can create the intended shape.
It reduces the need for multiple handling, processing steps, and other secondary operations like machining. All this without compromising on the design and meets all the critical dimensions.
Therefore, the process efficiently creates precision components at the desired speed.
Some operations that may take place in a progressive die stamping cycle are punching, bending, coining, trimming, drawing, blanking, etc. Proper selection of the metal stamping operations and their sequence plays a crucial role in deciding the accuracy of the output.
DISCUSS YOUR PROGRESSIVE DIE STAMPING NEEDS? CONTACT US!
Factors that affect the quality of progressive die stamping parts
One of the crucial aspects that decides the quality of the output at high volumes is the progressive die design. Here are some key factors that help designers build a progressive die that creates metal parts as per customer requirements.
1. Material:
Metal sheets are subjected to high stress during the metal stamping process. For high volumes, the speed of operation is important, which further increases the stress on the metal sheet. Therefore, metal material must have enough good tensile strength suitable for the metal stamping process.
Also Read- Types of Progressive Tools That You Should Know About
2. Strip layout:
The goal is to make the most of the metal sheet without losing the accuracy of the design. Creating a strip layout is crucial as it affects the amount of scrap during the stamping process. Therefore, the strip layout must optimize material utilization.
A. Strip width: The strip width decides the number of passes required through the die. Therefore, it is designed to keep the number to a minimum to reduce the overall cycle time.
B. Die clearance: Die clearances are dependent on the tolerances. With proper die clearance, the die can produce parts with the required tolerances. This helps to prevent excess wear on the tooling.
C. Lubrication: Lubrication helps in reducing friction and hence the wear and tear of the die tooling. This way the manufacturers ensure the longevity of the tooling to produce parts with the required tolerances.
D. Production rate: While designing the progressive die, the production rate decides the type of tooling and the expected delivery time of the parts.
Common parts produced using progressive die stamping include:
- Automotive parts like Engine knock sensors, Car door lock actuators, transmission brackets
- Electronic components like circuit board shields and connectors
- Everyday products like garden tools, toys
- Consumer electronics like mobile covers
- Industrial components like gears and bearings
- Medical device parts like covers for implanted devices, and surgical instruments.
Progressive Die Stamping vs Transfer Die Stamping for High Volume
Transfer die stamping is similar to progressive die stamping, with a small yet significant difference in operation. Both metal stamping techniques incorporate more than one stamping operation at one go. The difference lies in the execution. The workpiece never gets detached from the metal strip until the last stage during the progressive die stamping, whereas in transfer die stamping workpiece gets detached after every operation.
Since metal pieces get transferred between more than workstations, the time to create a metal part is more in transfer die stamping when compared to progressive die stamping. This makes the latter a preferred option for high-volume metal part production orders.
Also Read- Progressive Stamping Die Design Tips
Final thoughts
The best way to ensure the quality and accuracy of metal parts is to choose a progressive die metal stamping manufacturer like us. We use state-of-the-art tooling techniques and have an expert design team that works in unison with the engineers to ensure the selection of the right materials and accuracy to the metal part geometry.
Ujjwal handles crucial roles like AGM Marketing, researcher, and is an author for KDDL – Eigen. He currently works with Eigen for implementing proven techniques and strategies for marketing plans on online and offline platforms. An expert in efficiently executing SEO, SEM, email marketing, social media marketing, PR marketing, Print campaigns, etc. Ujjwal has coordinated an efficient marketing team on various creative campaigns and programmatic buying to support various digital cross-promotion efforts. Implement efficient search optimization strategies with the help of collateral material and metrics.
In his former years, Ujjwal has years of experience in a managerial role for several reputed companies. His years of experience combined with the flair of writing help him come up with result oriented strategies for Eigen.